VIBRATING MICROENGINES FOR POWER GENERATION AND
MICROSYSTEMS ACTUATION |
|
home |
|
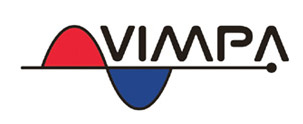 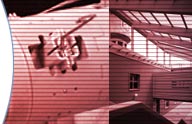 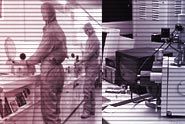 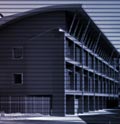 |
|
| |
|
 |
|
 |
|
|
 |
|
|
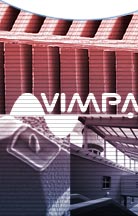 |
 |
Scenario
The challenge addressed by VIMPA is to develop usable
microsystems able to effectively power a wide range
of devices. There are several fields waiting for high
energy density power supply.
The
first domain is portable electronics, including for
example cellular phones, laptop computers, camcorders
and other consumer devices. In fact, we are observing
a real discrepancy between what is available to the
user and what should be the real performance of power
supplies. A laptop or a digital camera, for example,
have a typical autonomy of some (few) hours between
recharges, while a day-based autonomy should be reached
for an effective operation. Optimising power consumption
is evidently only an incremental and partial solution,
because of the high performances more and more expected
from new devices (e.g., wide LCD screens, powerful CPUs).
Dramatically increasing the energy density in electrochemical
batteries seems not to be a realistic issue, as proven
by the trend in results obtained by batteries companies
in the last years, where the density of 1MJ/Kg seems
to be an asymptotic value.
The second domain of interest regards systems able to
perform autonomous tasks without being connected to
a power cord or being constrained in a spatial location
where energy can be delivered both trough docking stations
or via wireless means. A challenging example is the
one of field microrobotics, where swimming,
locomoting or even flying microsystems can be exploited
for environmental inspection.
A third field addresses biomedical devices for health
assistance requiring high energy density and autonomy.
The most challenging example is maybe represented by
artificial heart, but also other biomedical systems
would take advantage from new, high performance power
cells, like autonomous microcapsules.
The above mentioned needs led to a wide research effort
in two main areas where a discontinuity in power generation
is expected: the one of fuel cells and the one of Power
MEMS. Just for reference also nuclear energy has been
considered as a long term candidate for power generation
in small systems, and in the USA a small category of
funding has been allocated for this activity by the
Nuclear Engineering Education Research (NEER) at the
Energy Department.
State of the Art in Power
MEMS
In the area of Power MEMS several micro-engine development
programs are underway. These include both microturbines
and positive displacement micromachines. These projects,
mentioned in the following paragraph, are moved by the
common motivation to replace batteries with integrated
packages composed of an engine-generator, a control
unit and a fuel tank. As already mentioned, the rationale
for developing micro-engines is rooted in energy density;
hydrocarbon fuels such as propane, have a lower heating
value of approximately 46 MJ/Kg. Batteries on the other
hand, have energy densities of 1 MJ/Kg at most. Consequently
an engine-generator would only need to have an overall
fuel conversion efficiency of 2.5 % to surpass any battery.
Of note, the overall fuel conversion efficiency of the
smallest mass-produced model airplane engine (0.16 cm3
displacement, absolutely not optimized regarding consumption)
is better than 4%. In addition, power MEMS can always
produce power as long as fuel is available, they can
be recharged (i.e., refilled) in a very fast time and
they do not pose a disposal problem when they need to
be replaced because they do not contain dangerous or
polluting components, only simply structural and electrical
parts. Finally, microengines can be used in two other
ways than as electrical generators: directly as prime
movers, thus eliminating the need for electrical actuators,
or as a source for compressed gas, enabling power pneumatics
in microsystems or microjet technology.
Microturbines have been developed in USA under DARPA
funding, in Japan and in Europe, but the problem of
high rotating speeds and bearings overheating restricted
experimental devices to be mainly operated using cold
compressed air.
Regarding burners for turbomachinery, complex combustors
are being developed in order to overcome the problem
of quenching in the micro domain, consisting in tortuous
burners with recirculation of thermal energy from the
combustion products to preheat the reactants. Also the
use of catalyst has been explored, exploiting expensive
platinum coated microstructures.
As a general remark, micro turbomachinery is still in
a very early stage, where individual components are
being developed but no real power MEMS have been integrated
yet.
On the other hand, a very promising approach is represented
by positive displacement micromachines, where thermal
energy does not have to be converted into kinetic energy
of the fluid. This is particularly advantageous when
dimensions are scaled down to the sub-millimetre scale,
avoiding pressure losses caused by the leading role
played by drag forces with respect to inertial forces
(low Reynolds numbers), which is a typical problem in
microturbines, whose efficiencies are in the order of
15 %.
Furthermore, in these systems combustion is not critical,
thanks to the possibility of increasing for a short
time the pressure and the temperature of the fluid by
exploiting a sudden compression. In fact at the University
of Minnesota the feasibility of micro-combustion based
on Homogeneous Charge Compression Ignition (HCCI) was
proven. It is interesting to observe that, following
these considerations, the industrial partner of the
research project, Honeywell Inc., filed a patent for
a microcombustion engine (US pat. n. 6276313). However
the proposed architecture exploited by the inventors
consists of a free-piston engine, a working principle
derived from macro engines. In this system the moving
parts (pistons) are sliding in a frame and they have
to provide sealing in order to obtain the adequate levels
of compression and to open and close the ports for gas
exchange, similarly to two strokes engines. Two requirements
are evidently involved: the low friction and the good
sealing. It is clear that the only technological way
to fit both issues is to fabricate coupling surfaces
with extremely good finishing, which is a very challenging
if not impossible task in the microdomain. A similar
approach, using sliding pistons, has been also adopted
very recently in Japan.
Power MEMS vs. Fuel Cells
Fuel cells presently are either very sensitive to fuel
impurities (such as CO in polymer-based fuel cells operating
on H2) or require very high operating temperatures,
which delay startups and cause shortened service life
due to thermal cycling stresses. Extensive research
has determined methanol to be the best choice but this
technology still needs development and currently no
solutions for mass production have been developed.
Also from an energetical point of view fuel cells are
still not very effective. Last results in industrial
research (Toshiba Corp., Japan) allowed companies to
give specifications for next generation of fuel cells,
to be introduced on the market in 2004. In particular
the best product is a Toshiba direct methanol fuel cell,
having a weight (excluding fuel tank) of 900 gr., with
an output of 12W and a Specific Fuel Consumption (SFC)
of 2·10-7 Kg/J. If this result is compared with
mini-generators for personal power need based on HCCI,
conclusions are very interesting. In fact a prototype
of electrical generator exploiting a mini HCCI engines
has the following characteristics: weight of 2.3 Kg,
output electrical power of 500 W, specific fuel consumption
of 1.7·10-7 Kg/J. It is therefore clear that
miniaturization is really welcome for HCCI engines. |
|
|
|
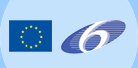 |
Project
funded by the European Commission under the NEST (New and
Emerging Science and
Technology) activity of the Sixth Framework Programme
(FP6), contract No. 511889
www.cordis.lu/nest |
|
|
|